10のはなし
ムーンスターは、使われてこそ価値のあるものをつくりたいと思っています。1873年創業。足袋の仕立てからものづくりを始めた私たち。以来、そして今、ものをつくるときに大切にしていることがあります。具体的なエピソードもまじえ、10のはなしにまとめました。
- 01 つながる、つづく、靴づくり
- 02 1から10まで靴をつくる
- 03 電車も開発室
- 04 手貼り靴
- 05 丁金
- 06 「焼き物みたいですね」
- 07 1足に6種類のゴム
- 08 機械靴
- 09 〝のり〟という素材
- 10 つくる人にやさしい場所

01 つながる、つづく、靴づくり
誰かがやっているから。時代的に流行っているから。
そういうものづくりは、理想ではありません。
明治初期にはじめてつくった、座敷足袋。
日本に暮らす人なら誰でも一度は履いたことのある学校の上履き。
日本人の足型に合わせたウォーキングシューズ。
成長過程の足を支える子ども靴。
過去に生産されていたトレーニングシューズを
現代に再現したスニーカー。
150年間、時間と手間をかけて
つくってきた靴と、靴を履く人たちの暮らし。
その中に、ムーンスターの哲学と技術のすべてがあります。
誰かに勝つためではなく、流行を追うのでもなく。
創意工夫の積み重ねを、次の靴づくりにつなげています。
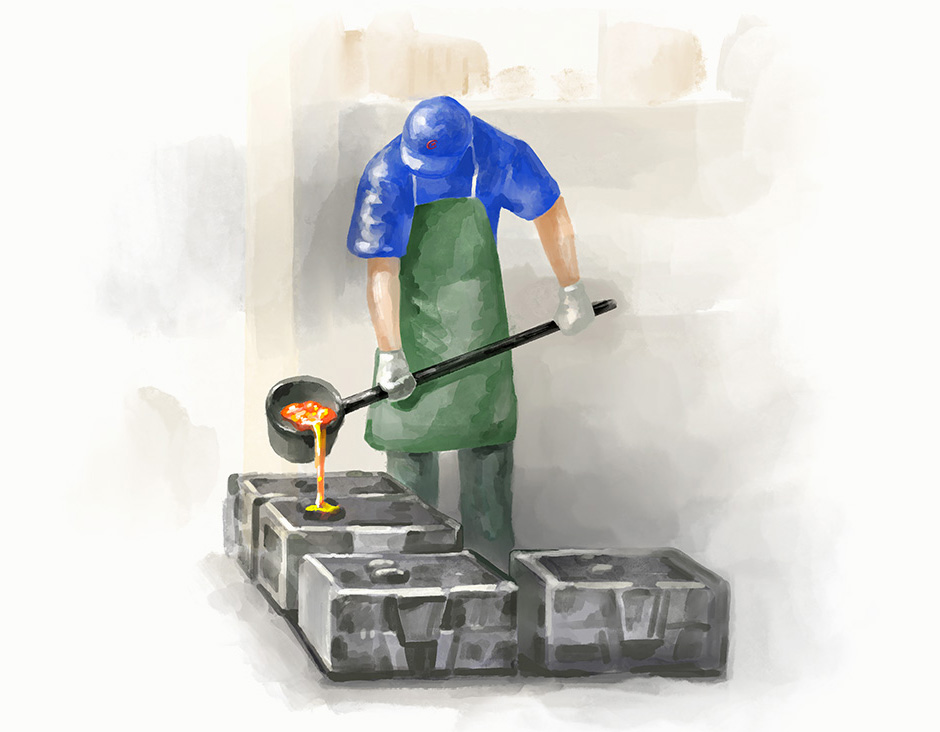
02 1から10まで靴をつくる
靴づくりの工程は数え切れないほどありますが、
すべてを自分たちでできなければ、
本当につくりたい靴はつくれないと思っています。
靴づくりの「1」は、ラスト(靴型)。
木の塊から足型を削り出した後、
靴の製造工場に併設された鋳物工場で
アルミニウムを800℃で溶かし、型に流し込んでつくります。
自分たちの手でやることで、成分の状態や数値が把握できるため、
アルミニウムを何度でも再利用して新しいラストをつくれます。
今までにつくったラストは、約16,000種類。
工程を細分化し、専門の会社にお願いすれば
効率的かもしれませんが、
自分たちが信じるものづくりをつづけます。
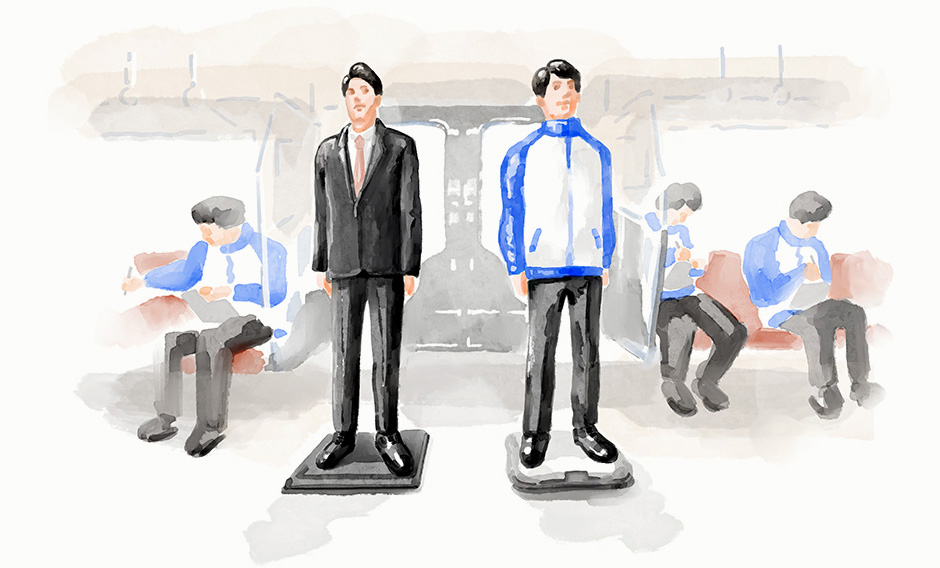
03 電車も開発室
毎日履く靴。開発のヒントは暮らしの中にしかありません。
たとえば、本物の電車を1両貸切にして走らせて
実験をしたことがありました。
当時発売間近だったビジネスシューズ。
ビジネスパーソンの多くが利用する電車でも、
バランスを崩さずに履ける靴としての完成度があるのか。
重心を測定できる特別な機材を持ち込み、
ガタンゴトンと揺れる車内で実験。
使う人の暮らしをよく観察し、
想定される環境やシーンで繰り返し使用してみる。
そういうものづくりをしています。
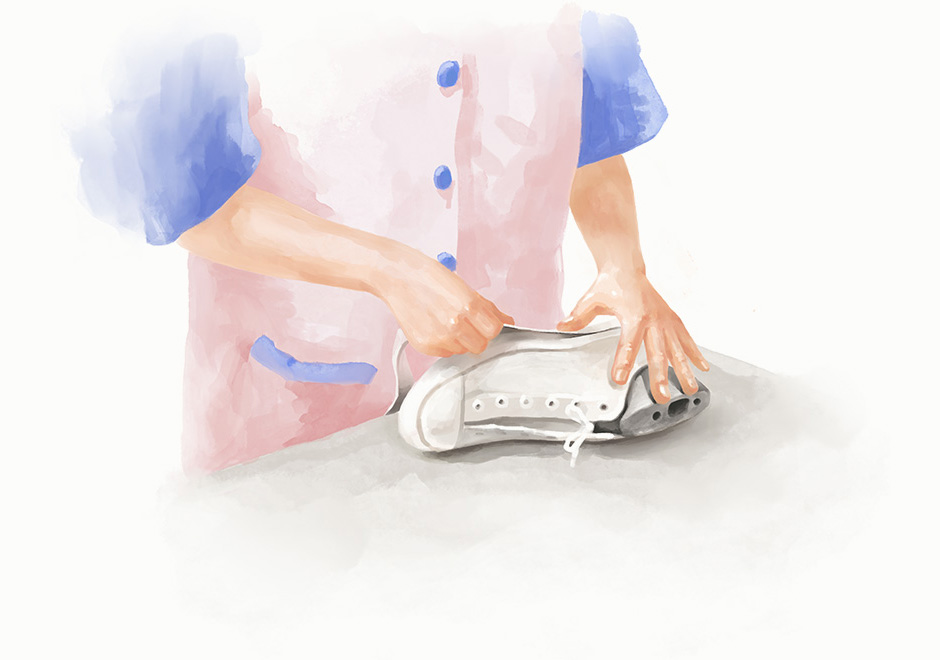
04 手貼り靴
久留米工場には、
ゴムの生地を手作業で貼り付けてつくる靴があります。
ゴムを裁断し、ハケでのりを塗り、技術と感覚でゴムを貼る。
そうしてでき上がった靴は、ひとつひとつよく見てみると
ゴムのカッティングが微妙にちがったり、凹凸があったり。
今の時代、いつ買っても、どれを買ってもまったく同じものが
手に入るのはありがたいことですが、
同じ商品でもひとりひとりちがう作り手のあたたかみが
感じられるものも嬉しい。
作り手と使い手が商品を通してつながる関係は、
工場からはじまっています。
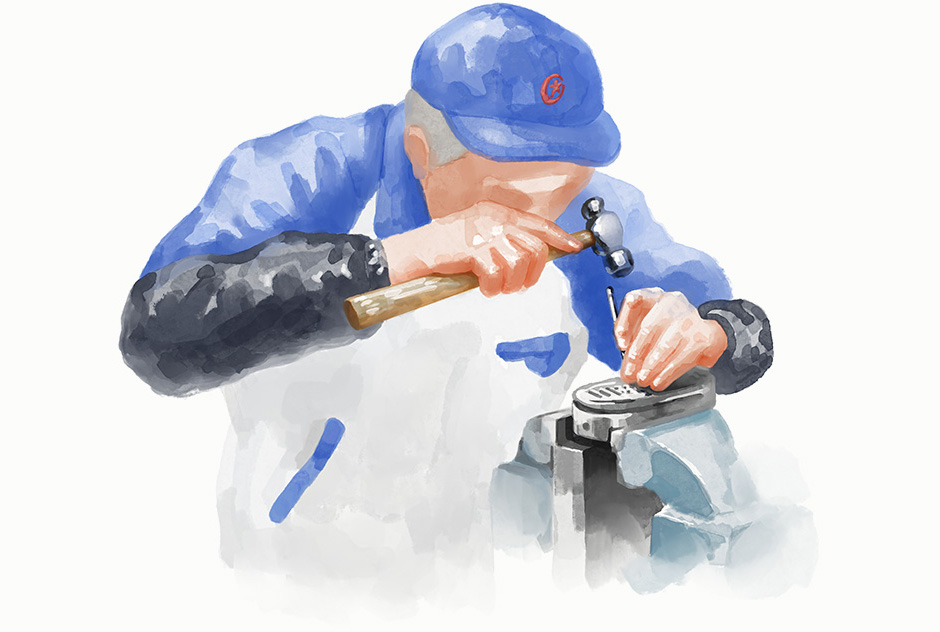
05 丁金
丁金(ていきん)とは、のみとハンマーを使い、
金属を彫刻すること。
久留米工場では、靴底のゴムのデザインになる金型を、
手打ちでつくっています。
目的によっては機械を使ったほうが、速く、
きれいにつくれるため、適している工程もありますが、
どうしても無機質で余白のないものになってしまうことも
少なくありません。
靴底は靴の佇まいを決める大切な要素のひとつ。
人の手で打ち、角に自然な丸みを出すことで、
あたたかみが感じられる靴に仕上がります。
職人が技術を習得するのに10年。
手打ちの作業そのものにも時間がかかりますが、
このやり方でしか出せない良さをつないでいます。
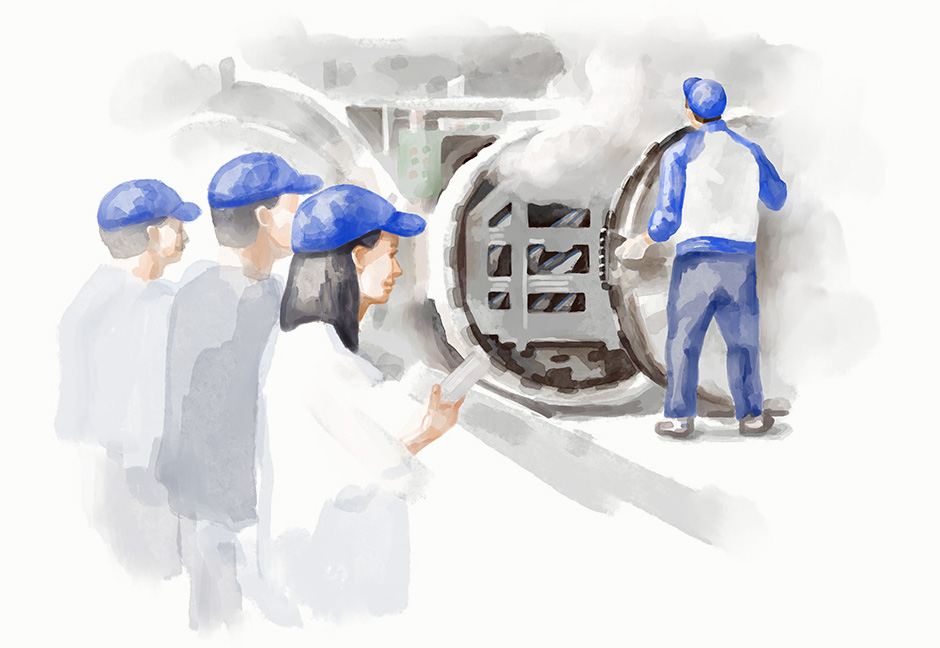
06 「焼き物みたいですね」
Shoes Like Pottery(焼き物のような靴)というコンセプトは、
工場見学をされた方から思わずこぼれた一言からできました。
ゴムに配合した硫黄を化学反応させることで、
耐久性や弾性を強化するヴァルカナイズ(加硫)製法。
その最終工程で使ってきた“加硫缶”を、
“窯”に見立て、“焼き物”と表現する。
その自然な発想に、はっとさせられました。
ものづくりは、作り手だけでできるものではありません。
使い手となる人の、正直な気持ちを聞き、
使い心地のいいものを一緒につくっていきたいと思います。
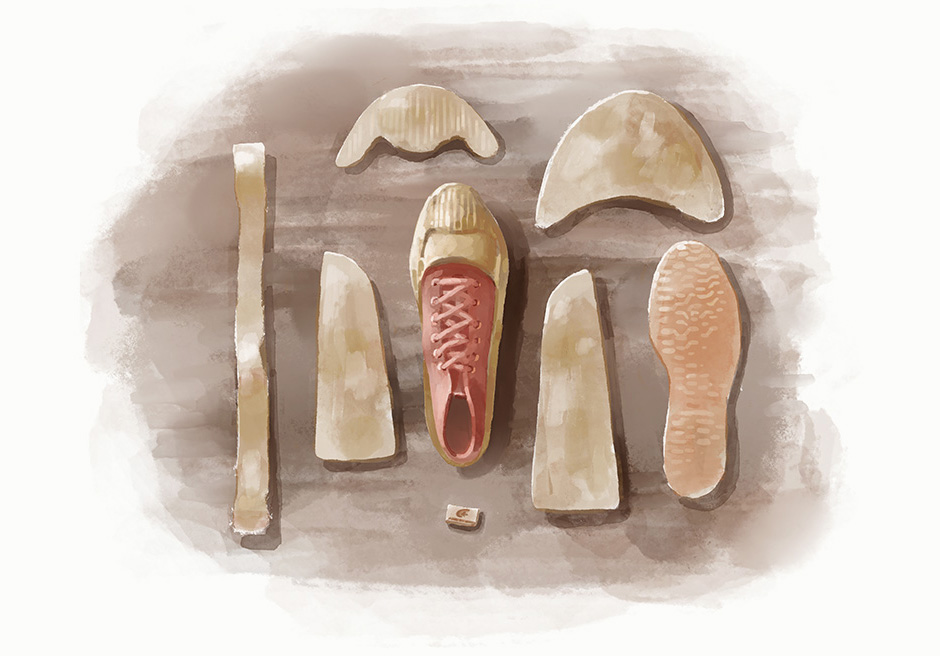
07 1足に6種類のゴム
いいゴムとは、履く人の用途や環境で役割を全うするゴム。
人の暮らし方が多様なことを考えると、原料の配合比率にも、
靴のどの部分にどんなゴムを組み合わせるかにも、
際限はありません。
全天候型の靴としてつくった“ALWEATHER”には、
6種類のゴムが採用されました。
かかとをホールドする「月形ゴム」。
靴構造をしっかりと支える「テープゴム」。
足に負担をかけないために側面を覆う「胴ゴム」。
摩耗しにくく適度に柔らかい「底ゴム」。
クッション性が良くスポンジのような「中底ゴム」。
布とそれぞれのゴムをくっつける「接着ゴム」。
薬品の配合比率、混ぜ方、熱を加える加硫工程での
温度との相性など、試行錯誤を繰り返すことで、
使われてこそ価値のある靴をつくっています。
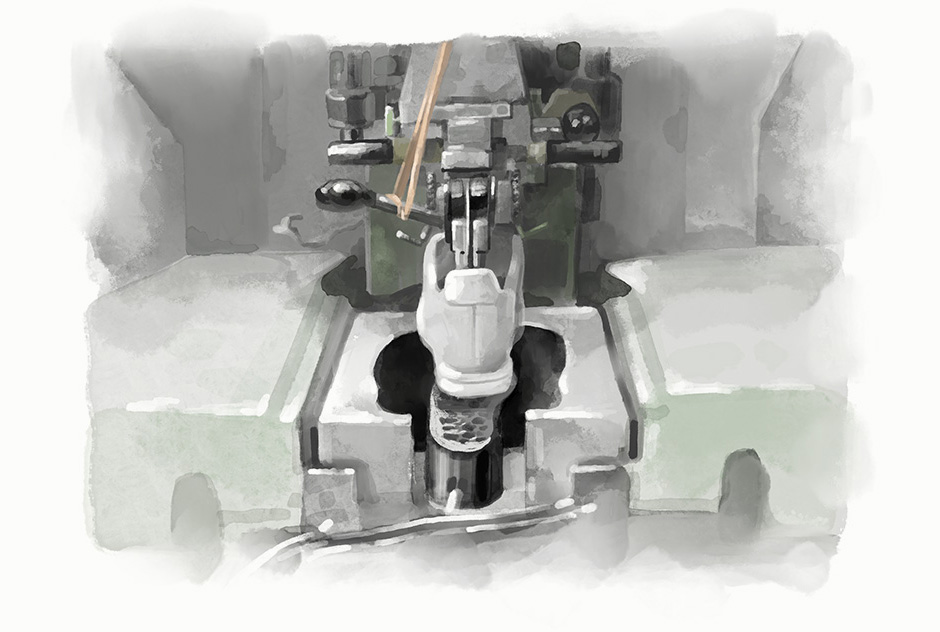
08 機械靴
手貼り靴に独特の良さがあるのと同じく、
機械でつくる靴にも良さがあります。
久留米工場では、国内では希少となった
インジェクション製法(機械靴)用の大規模な設備が健在です。
底の成型と接着を同時に行って量産できるため、
年間約70万足を生産する学生靴をはじめ、
作業靴や長靴などの普遍的なデザインに適した設備です。
日常でハードに使われる靴にとって大切なのは耐久性。
その中で重要な役割を果たすのがPU(ポリウレタン)です。
ムーンスターでは、
PUの短所である水への弱さ(加水分解)を克服した
“ベステック”という素材を開発し、インジェクション製法と
組み合わせることで、長く使える靴をつくっています。
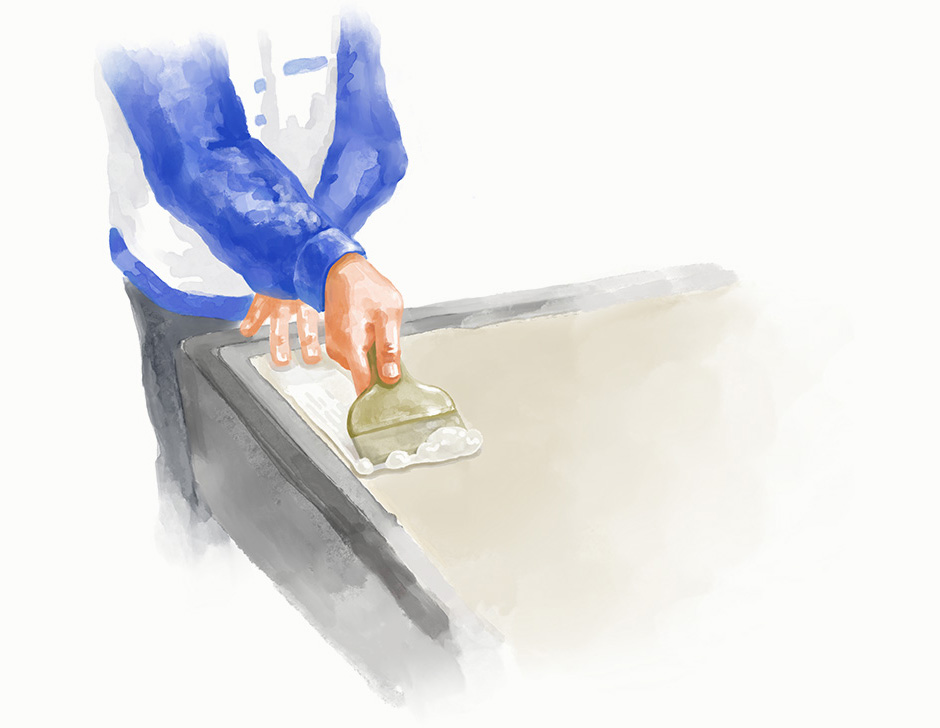
09 “のり”という素材
のりは、何かと何かをくっつけるもの。
靴づくりでも、底とアッパーを接着するのに
重要な役割を果たします。
これまで接着だけに使ってきたのりに、別の使い道はないか。
試行錯誤をはじめてみて気付いたのが、その塗膜性です。
のりをアッパーの生地にヘラで塗り込み、
生地の目に染み込ませると、乾いたのりは膜となり、
靴の強度と防水性を高めることが分かりました。
自分たちがつくる靴が、使われてこそ価値があるのと同じで、
素材も使われてこそ価値がある。
使い方をよく考えることで、資源を無駄にしない
ものづくりにもつながります。
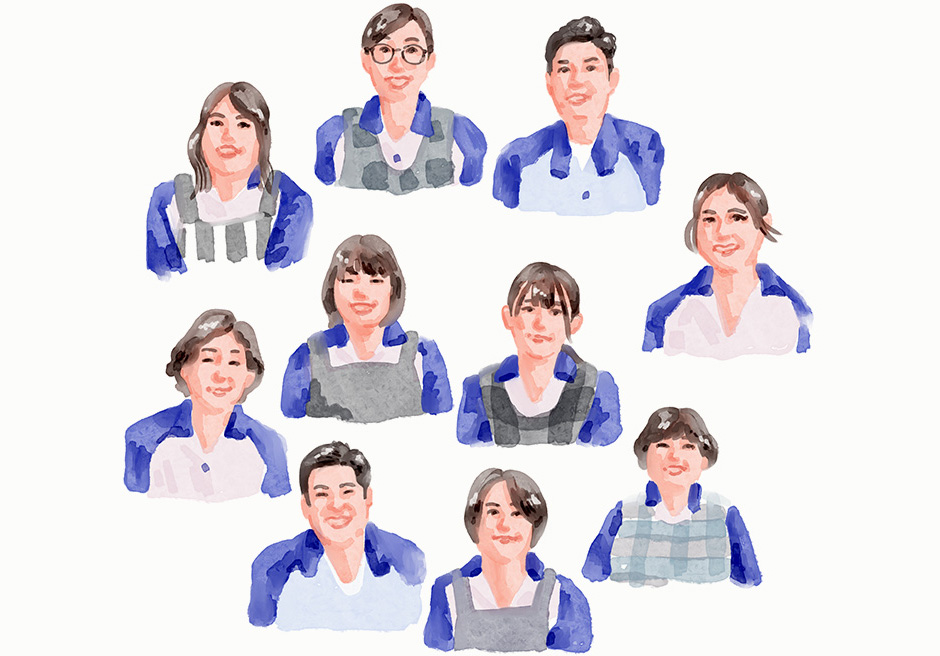
10 つくる人にやさしい場所
久留米工場で働く人は、ほとんどが地元、筑後地区の人たち。
だから、家族や親戚のように「数子さん」や「まささん」など、
下の名前やあだ名で呼び合う風習があります。
私たちは、地域で受け継いできた場所を、
働きたいと思ってもらえる場所にするための工夫をしてきました。
たとえば、中敷にロゴを印刷するインクを、
シンナーを含まない水溶性のものにしたり。
機械にキャスターを付けて、動かせる状態にしておくことで、
その人の成長に合わせて自由に
ラインを組み替えられる仕組みをつくったり。
工場見学でお客様が通るラインの人を定期的に代え、
やりがいを感じてもらったり。
人と地域とものづくりの循環を絶やさないために、
できることをつづけます。